In today's rapidly developing solid waste treatment industry, efficient and precise metal processing technology has become the core competitiveness for improving resource regeneration efficiency. Faced with the processing pain points of high hardness, complex shapes, and sensitive properties of waste metal materials, traditional cutting methods often fail to balance processing accuracy and material integrity. This article delves into the technical characteristics of four major processes: wire cutting, water jet cutting, laser cutting, and plasma cutting, with a focus on revealing the unique advantages of wire cutting technology in the field of precision tool manufacturing.
As a leading enterprise in the field of shredder tool manufacturing, we rely on a cluster of dozens of CNC wire cutting machines and technical accumulation to build a full-chain solution from precision processing to intelligent control. We continuously provide the industry with tool products that combine high precision and high reliability, promoting the evolution of solid waste treatment equipment towards high-end and intelligent directions.
Wire cuttingWire cutting technology, also known as electrical discharge machining (EDM), is a precise machining method that removes material through electrical spark discharge. In the solid waste treatment industry, the advantage of wire cutting lies in its ability to accurately cut high-strength and high-hardness materials, which is crucial for processing various waste metals. In addition, the high precision of wire cutting means that it can cut complex shapes, which is very useful for manufacturing customized tools and components for solid waste treatment. During the wire cutting process, the tool deformation is small, which helps to maintain the original performance of the tool. This is an important advantage for solid waste treatment equipment that requires long-term operation and high reliability.
Water jet cuttingWater jet cutting, also known as water knife, uses high-pressure water flow to cut materials, and sometimes abrasives are added to enhance the cutting ability. This technology is a cold cutting method that does not produce a heat-affected zone and is suitable for cutting materials that are sensitive to temperature. In solid waste treatment, water jet cutting can be used to cut large or thick waste materials. However, compared with wire cutting, its cutting accuracy is lower and the speed is slower, which may limit its use in applications that require high precision and rapid processing.
Laser cuttingLaser cutting uses a high-energy laser beam to melt or vaporize the material to achieve cutting. This technology is known for its speed and high precision and is suitable for mass production. In the solid waste treatment industry, laser cutting can be used to cut a variety of materials, including metals and non-metals. However, the cost of laser cutting equipment is high, and thermal deformation may occur during the cutting process, which may require additional processing steps to correct, increasing costs and time.
Plasma cuttingPlasma cutting uses the heat of a high-temperature plasma arc to melt the material, and then the molten material is removed by a high-speed plasma stream to form a cut. This technology is suitable for cutting a variety of metal materials, especially when rapid cutting of thick materials is required. In the solid waste treatment industry, plasma cutting can be used to process large metal waste. However, the accuracy of plasma cutting is relatively low, and the cutting surface may require secondary processing, which may increase additional costs and time.
The advantages of wire cutting in the solid waste industryIn the solid waste treatment industry, the advantage of wire cutting lies in its ability to provide high-precision and high-quality cutting, which is crucial for manufacturing precise tools and components. The cold cutting characteristics of wire cutting mean that it does not produce thermal deformation, which is very important for maintaining the original performance of the material. In addition, wire cutting can process materials with high hardness, which is particularly useful for waste metals commonly encountered in solid waste treatment. These characteristics of wire cutting make it a very valuable tool in the solid waste treatment industry, especially in applications that require high precision and reliability.
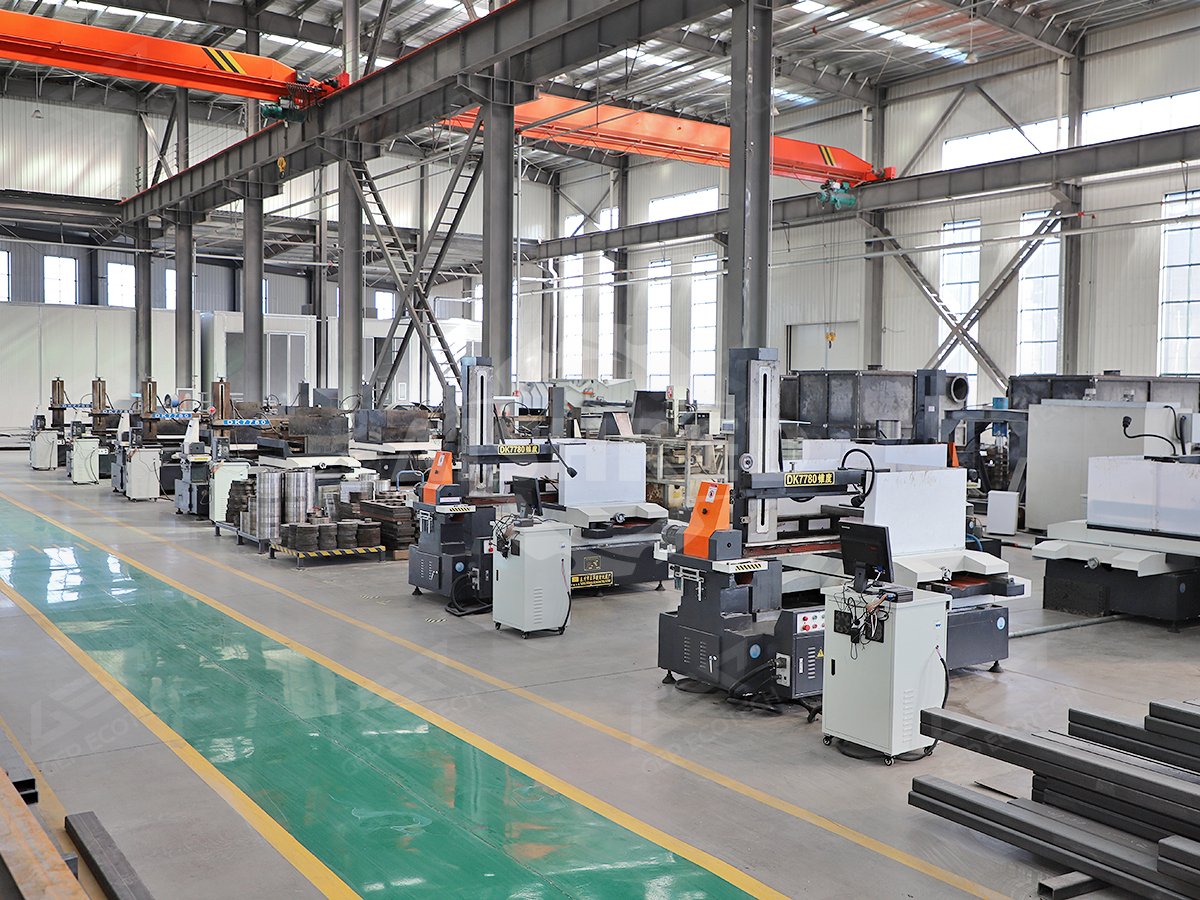
In the field of precision machining of shredders, GEP ECOTECH has shown significant industry advantages. The dozens of CNC wire cutting machines we possess enable us to flexibly meet production needs of different scales. Whether it is small-batch customized production or large-scale batch orders, we can complete them efficiently and stably. During the production process, our strict quality control covers every step from the selection of raw materials to the processing of finished products, ensuring that each step meets high standards. Our operating team is composed of experienced professionals who can skillfully operate the equipment to achieve high-precision cutting results. In addition, the advanced production management system we use monitors the entire production process in real time, ensuring that any potential production problems can be quickly responded to and resolved.